Activated carbon is a highly porous substance that attracts and holds organic chemicals inside it. The media is created by first burning a carbonaceous substance without oxygen which makes a carbon “char”. Next, the “char” is treated chemically or physically to develop an interconnected series of “holes” or pores inside the carbon. The great surface area of this internal pore network results in an extremely large surface area that can attract and hold organic chemicals.
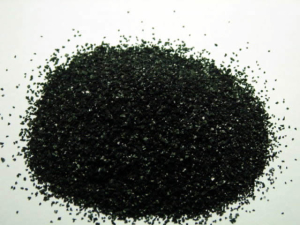
The primary raw material used for activated carbon is any organic material with a high carbon content (coal, wood, peat, coconut shells). Granular activated carbon media is most commonly produced by grinding the raw material, adding a suitable binder to give it hardness, re-compacting and crushing to the correct size.
The carbon-based material is converted to activated carbon by thermal decomposition in a furnace using a controlled atmosphere and heat. The resultant product has an incredibly large surface area per unit volume, and a network of submicroscopic pores where adsorption takes place.
The walls of the pores provide the surface layer molecules essential for adsorption. Amazingly, one pound of carbon (a quart container) provides a surface area equivalent to six football fields.
Almost all materials containing a high fixed carbon content can potentially be activated. The most commonly used raw materials are coal (anthracite, bituminous and lignite), coconut shells, wood (both soft and hard), peat and petroleum based residues.
Many other raw materials have been evaluated such as walnut shells, peach pits, babassu nutshell and palm kernels but invariably their commercial limitation lies in raw material supply. This is illustrated by considering that 1,000 tons of untreated shell type raw material will only yield about 100 tons of good quality activated carbon.
Most carbonaceous materials do have a certain degree of porosity and an internal surface area in the range of 10-15 m2/g. During activation, the internal surface becomes more highly developed and extended by controlled oxidation of carbon atoms – usually achieved by the use of steam at high temperature.
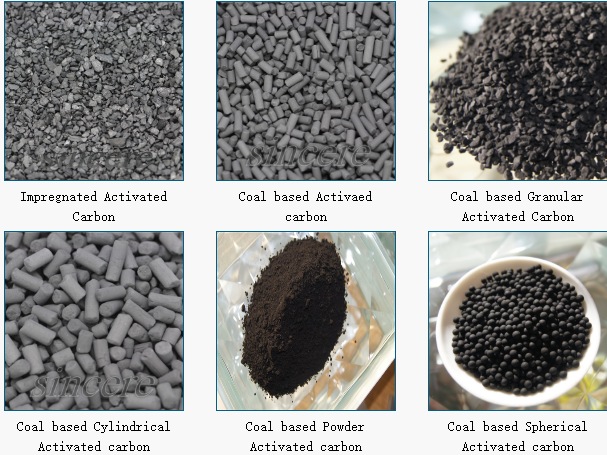
After activation, the carbon will have acquired an internal surface area between 700 and 1,200 m2/g, depending on the plant operating conditions.
The internal surface area must be accessible to the passage of a fluid or vapor if a potential for adsorption is to exist. Thus, it is necessary that an activated carbon has not only a highly developed internal surface but accessibility to that surface via a network of pores of differing diameters.
As a generalization, pore diameters are usually categorized as follows:
- micropores <40 Angstroms
- mesopores 40 – 5,000 Angstroms
- macropores >5,000 Angstroms (typically 5000-20000 A)
During the manufacturing process, macropores are first formed by the oxidation of weak points (edge groups) on the external surface area of the raw material. Mesopores are then formed and are, essentially, secondary channels formed in the walls of the macropore structure. Finally, the micropores are formed by attack of the planes within the structure of the raw material.
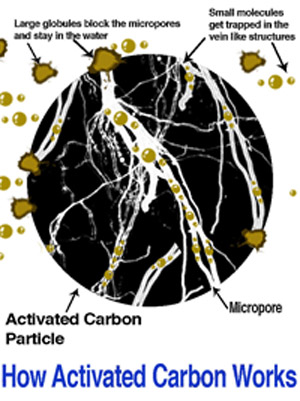
All activated carbons contain micropores, mesopores, and macropores within their structures but the relative proportions vary considerably according to the raw material.
A coconut shell based carbon will have a predominance of pores in the micropore range and these account for 95% of the available internal surface area. Such a structure has been found ideal for the adsorption of small molecular weight species and applications involving low contaminant concentrations.
In contrast wood and peat based carbons are predominantly meso/macropore structures and are, therefore, usually suitable for the adsorption of large molecular species. Such properties are used to advantage in decolorization processes.
Coal based carbons, depending on the type of coal used, contain pore structures somewhere between coconut shell and wood.
In general, it can be said that macropores are of little value in their surface area, except for the adsorption of unusually large molecules and are, therefore, usually considered as an access point to micropores.
Mesopores do not generally play a large role in adsorption, except in particular carbons where the surface area attributable to such pores is appreciable (usually 400 m2/g or more).
Thus, it is the micropore structure of an activated carbon that is the effective means of adsorption. It is, therefore, important that activated carbon not be classified as a single product but rather a range of products suitable for a variety of specific applications
Adsorption/Adsorbents/Activated Carbon
Since adsorption is a comparatively specialized technology, a capsule definition of terms may be helpful. Adsorption is a surface phenomenon, in which molecules of adsorbate are attracted and held to the surface of an adsorbent until an equilibrium is reached between adsorbed molecules and those still freely distributed in the carrying gas or liquid. While the atoms within the structure of the adsorbent are attracted in all directions relatively equally, the atoms at the surface exhibit an imbalanced attractive force which the adsorbate molecules help to satisfy. Adsorption can then be understood to occur at any surface, such as window glass or a table top. The characteristic which typifies an adsorbent is the presence of a great amount of surface area; normally via the wall area or slots, capillaries or pores permeating its structure, in a very small volume and unit weight.
The type of adsorption which is dependent primarily on surface attraction, in which factors such as system temperature, pressure, or impurity concentration may shift the adsorption equilibrium, is given the further classification of physical adsorption. The electronic forces (Van der Waal’s forces) responsible for adsorption are related to those which cause like molecules to bind together, producing the phenomena of condensation and surface tension. Conceptually, some prefer the analogy of physical adsorption being like iron particles attracted to, and held by, a magnet. Physical adsorption is the most commonly applied type, but an important sub-classification is chemisorption. Chemisorption refers to a chemical reaction between the adsorbate and the adsorbent , or often reaction with a reagent which may be impregnated on the extensive adsorbent surface (see Impregnated Carbons, below). Thus physical adsorption/desorption retains the chemical nature of the adsorbate, while chemisorption alters it.
The surface phenomenon of adsorption may now be contrasted with apsorption, in which one material intermingles with the physical structure of the other; for example, phenol dissolving into fibers of cellulose acetate (absorption) versus being adhered by surface attraction to the outer layer of the fibers (adsorption).
Activated charcoal) is an adsorbent derived from carbonaceous raw material, in which thermal or chemical means have been used to remove most of the volatile non-carbon constituents and a portion of the original carbon content, yielding a structure with high surface area. The resulting carbon structure may be a relatively regular network of carbon atoms derived from the cellular arrangement of the raw material, or it may be an irregular mass of crystallite platelets, but in either event the structure will be laced with openings to appear, under electron micrographic magnification, as a sponge like structure. The carbon surface is characteristically non-polar, that is, it is essentially electrically neutral. This non-polarity gives the activated carbon surface high affinity for comparatively non-polar adsorbates, including most organics. As an adsorbent, activated carbon is this respect contrasts with polar desiccating adsorbents such as silica gel and activated alumina. Granular Activated carbon will show limited affinity for water via capillary condensation, but not the surface attraction for water of a desiccant.
Activity Level
Activity level is often expressed as total surface area per unit weight, usually in square meters per gram. This total exposed surface will typically be in the range of 600-1200 m2/g. Toward the higher end of this range, one might better visualize one pound, about a quart in volume, of granular activated carbon with a total surface area of 125 acres.
To be useful in adsorption, surface area must be present in openings large enough to admit the adsorbate molecule(s). To provide some guidance on this topic, and for quality control purposes, the carbon industry has developed additional standardized vapor and liquid adsorption tests, using adsorbates of varying molecular size and chemical nature such as iodine, phenol, methylene blue, carbon tetrachloride, benzene and the color in standard black strap molasses. However activity level is measured, it is most meaningful when considered with additional characteristics described in the following sections.
Pore Structure
While openings into the carbon structure may be of various shapes, the term “pore,” implying a cylindrical opening, is widely used. A description of the minute distances between walls of these pores, normally expressed as a function of the total surface area or total pore volume presented by pores of various “diameters,” is the pore structure curve. The following sketches show some sample pore structure curves and what approximate pore shapes are described by the curves. Please note that the average pore shape depicted is derived from a summation of pores of various sizes and shapes. Thus no pore within the activated carbon is likely to have precisely the average shape, but the granular activated carbon overall will often perform as if all its surface area were in pores of that shape.
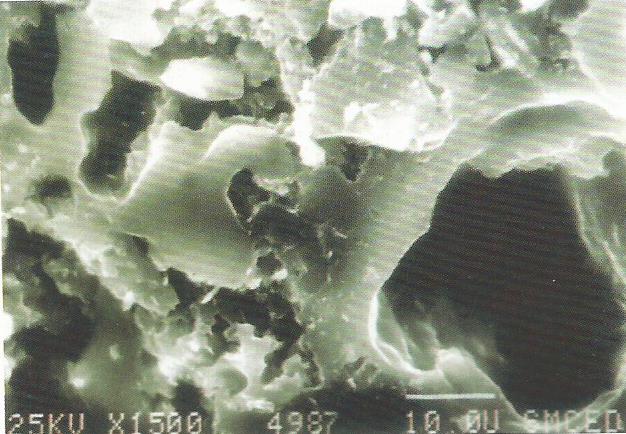
The smallest diameter pores make up the micropore structure, and are the highest adsorption energy sites. Microporosity is helpful in adsorbing lower molecular weight, lower boiling point organic vapors, as well as in removing trace organics in water to non-detectable levels. Larger pore openings make up the macroporosity, which is useful in adsorbing very large molecules and aggregates of molecules, such as “color bodies” in raw sugar solutions. Another important function of the macropore structure is in assisting diffusion of fluids to adsorption sites in the interior of the carbon particle.
Given the above, pore structure. (1) would be effective in adsorbing high volatility solvents, for certain types of odor control, and in removing trace organics from water; the latter with the liability of marginal diffusion characteristics. Pore structures along the lines of. (2) offer a good balance of selectivity for molecules of various sizes, ability to reduce vaporous and liquid contamination to ultra low levels, and good diffusion characteristics. Structure (3) would allow excellent diffusion and can accommodate very large molecular sizes, but has little micro- pore structure and would have very poor retentivity for most organics.
Activated carbon properties
Activated carbon is a non-hazardous carbon-bearing product with a porous structure and a very large internal surface area. The chemical structure of activated carbon can be defined as a crude form of graphite, with a random amorphous structure that is highly porous over a range of pore sizes, from visible cavities and gaps to those of molecular dimensions.
Treatment with activated carbon is based primarily on the phenomenon known as adsorption, in which molecules of a liquid or gas adhere to an external or internal surface of a solid substance. Activated carbon has a very large internal surface area (up to 1,500 m²/g) which makes it highly suitable for adsorption. Activated carbon can be impregnated with certain chemicals in order thus to enhance its properties for certain applications.
Applications:
Water and liquid applications for:
- municipal drinking water treatment (taste, odour and micro pollutant removal e.g. pesticides, …),
- domestic water treatment (in-line and cartridge filters),
- process water (de-chlorination and de-ozonation),
- ground water remediation,
- waste water treatment – tertiary treatment (trace organics and COD removal, deodourisation and decolourisation, powdered as bio-flock improvement in an aerobic or anaerobic biological waste water treatment plant, as an additive for physical- chemical treatments),
- raw material purification (purification of oils and fats, alcoholic and softdrinks, dyestuffs, …, decolourisation of sugar and glucose, food, chemicals, pharmaceuticals) and
- catalytic processes.
Air and gas applications for:
- air purification and environmental protection (removal of solvents and hydrocarbons, deodourisation, air conditioning, cooker hoods, flue gases, in powdered form the removal of dioxins, mercury and other trace elements from flue gases),
- cleaning process gases (removal of contaminants from hydrogen, natural gas, carbon dioxide, landfill gas, solvent recovery, …),
- respiration protection (gas masks, removal of harmful of toxic compounds),
- tank venting,
- ground water remediation,
- molecular sieves.
Is There A Difference Between Activated Carbon And Activated Charcoal?
Most people have a misunderstanding that there is a difference between activated carbon and activated charcoal. Both of these terms can and are used interchangeably. As well, active carbon is another similar word used for activated carbon and activated charcoal. All of these phrases are synonymous and commonly found in our field.
What Does Activated Carbon Do?
Activated carbon attracts and holds organic chemicals from vapor and liquid streams cleaning them of unwanted chemicals. It does not have a great capacity for these chemicals, but is very cost effective for treating large volumes of air or water to remove dilute concentrations of contamination. For a better perspective, when individuals ingest chemicals or are experiencing food poisoning, they are instructed to drink a small amount of activated carbon to soak up and remove the poisons.
What Will Activated Carbon Remove?
Organic chemicals are attracted to carbon the best. Very few inorganic chemicals will be removed by carbon. The molecular weight, polarity, solubility in water, temperature of the fluid stream and concentration in the stream are all factors that affect the capacity of the carbon for the material to be removed. VOCs such as Benzene, Toluene, Xylene, oils and some chlorinated compounds are common target chemicals removed through use of carbon. Other large uses for activated carbon are the removal of odors and color contamination.
What Is Activated Carbon Made From?
Granular activated carbon can be produced from various carbonaceous raw materials, each of which will impart typical qualities to the finished pro-duct. Commercial grades are normally prepared from coconut and other nut shells, bituminous and lignite coals, petroleum coke, and sawdust, bark and Other wood products.
In general, nut shells and petroleum cokes will produce very hard carbons with a pore structure characterized by.(1) above, coals a (2) type structure in comparatively hard carbons, and wood (3) structure in carbons lacking great crush and abrasion resistance. It should be emphasized that specific production techniques may yield carbons that depart from the norm of a given raw material.Here at General Carbon, we carry activated carbon made from bituminous coal, lignite coal, coconut shell and wood.