Activated carbon is made of high-quality coal, wood chips, fruit shells, coconut shells and other materials, and is refined by advanced process equipment. The production process of activated carbon is roughly divided into: carbonization → cooling → activation → washing and other refined processes. The shape of the finished product of activated carbon is roughly divided into: granule, columnar, powdery, etc.
Activated carbon is a processed, porous version of carbon that has many different uses, especially adsorption and chemical reaction needs for water and gas purification. Because activated carbon particles are so porous, they have very expansive surface areas tucked into the holes and tunnels all over their surface.
These areas can be filled with other materials for other purposes as well. For instance, in water purification, silver is mixed into the carbon pores in order to filter contaminants like mercury and organic arsenic from water for domestic drinking purposes.
Because carbon is produced from charcoal through a relatively inexpensive and simple series of activation processes, it can be had in great quantities for many applications.
The Carbon Manufacturing Process – How to Make Activated Carbon
The production process of activated, or active, carbon exists in two forms. A carbonaceous source, which can exist as coal, peat, or any organic carbonaceous material is carbonized, which means the pure carbon is extracted by a heating method known as pyrolysis. Once the material is carbonized, it needs to be oxidized, or treated with oxygen, either by exposure to CO2 or steam, or by an acid-base chemical treatment.
Carbonization
Carbonization is the process of taking a carbon-rich piece of material and converting it to pure carbon through heating. This heating process, called pyrolysis, comes from an ancient technique for making charcoal. Very dense carbonaceous material is used in the beginning, because the end result needs to be extra-porous for activated carbon purposes.
Carbon-rich material is placed in a small (relative to the amount of material) furnace and cooked at extreme temperatures topping 2000 degrees Celsius. What remains is usually 20-30 percent of the beginning weight, and consists of mostly carbon and a small percentage of inorganic ash. This is very similar to “coking,” a method of producing coke from charcoal, a type of carbon-based fuel.
Once the porous form of carbon is produced, it needs to undergo oxidization so it can be adsorbent. This can occur in one of two ways: gas or chemical treatment.
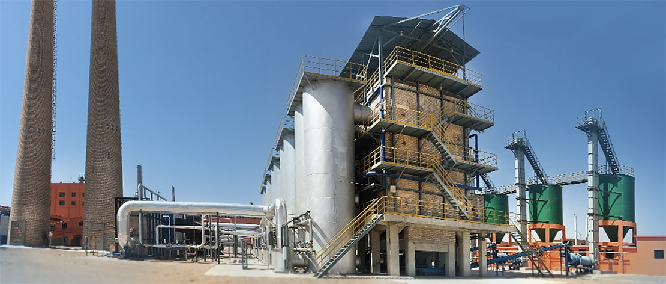
all carbonaceous materials can be converted into activated carbon,materials can be converted into activated carbon, although the properties of the final product will be different, depending on the nature of the raw material used, the nature of the activating agent, and the conditions of the carbonization and activation processes.
During the carbonization process, most of the noncarbon elements such as oxygen, hydrogen, and nitrogen are eliminated as volatile gaseous species by the pyrolytic decomposition of the starting material. The residual elementary carbonstarting material. The residual elementary carbon atoms group themselves into stacks of flat, aromatic sheets cross-linked in a random manner. These aromatic sheets are irregularly arranged, which leaves free interstices. These interstices give rise to pores, which make activated carbons excellent adsorbents.
During carbonization these pores are filled with the tarry matter or the products of decomposition or at least blocked partially by disorganized carbon. This pore structure in carbonized char is further developed andcarbon. This pore structure in carbonized char is further developed and enhanced during the activation process, which converts the carbonized raw material into a form that contains the greatest possible number of randomly distributed pores of various sizes and shapes, giving rise to an extended and extremely high surface area of the product.
The activation of the char is usually carried out in an atmosphere of air, CO2, or steam in the temperature range of 800°C to 900°C. This results in the oxidation of some of the regions within the char in preference to others, so that as combustion proceeds, a preferential etching takes place. This results in the development of a large internal surface, which in some cases may be as high as 2500 m2/g.
Gas Treatment
The activizing of carbon can be done directly through heating in a chamber while gas is pumped in. This exposes it to oxygen for oxidization purposes. When oxidized, the active carbon is susceptible to adsorption, the process of surface bonding for chemicals—the very thing that makes activated carbon so good for filtering waste and toxic chemicals out of liquids and gases. For physical gas treatment, the carbonization pyrolysis process must take place in an inert environment at 600-900 degrees Celsius. Then, an oxygenated gas is pumped into the environment and heated between 900 and 1200 degrees Celsius, causing the oxygen to bond to the carbon’s surface.
Chemical Treatment
In chemical treatment, the process is slightly different from the gas activization of carbon. For one, carbonization and chemical activation occur simultaneously. A bath of acid, base or other chemicals is prepared and the material submerged. The bath is then heated to temperatures of 450-900 degrees Celsius, much less than the heat needed for gas activation. The carbonaceous material is carbonized and then activated, all at a much quicker pace than gas activization. However, some heating processes cause trace elements from the bath to adsorb to the carbon, which can result in impure or ineffective active carbon.
Post Treatment Activated Carbon
Following oxidization, activated carbon can be processed for many different kinds of uses, with several classifiably different properties. For instance, granular activated carbon (GAC) is a sand-like product with bigger grains than powdered activated carbon (PAC), and each are used for different applications. Other varieties include impregnated carbon, which includes different elements such as silver and iodine, and polymer-coated carbons.
How Does Activated Carbon Work?
Physical adsorption is the primary means by which activated carbon works to remove contaminants from liquid or vapor streams. Carbon’s large surface area per unit weight allows for contaminants to adhere to the activated carbon media.
The large internal surface area of carbon has several attractive forces that work to attract other molecules. These forces manifest in a similar manner as gravitational force; therefore, contaminants in water are adsorbed (or adhered) to the surface of carbon from a solution as a result of differences in adsorbate concentration in the solution and in the carbon pores.
Physical adsorption occurs because all molecules exert attractive forces, especially molecules at the surface of a solid (pore walls of carbon), and these surface molecules seek to adhere to other molecules.
The dissolved adsorbate migrates from the solution through the pore channels to reach the area where the strongest attractive forces are located. Contaminants adsorb because the attraction of the carbon surface for them is stronger than the attractive forces that keep them dissolved in solution. Those compounds that exhibit this preference to adsorb are able to do so when there is enough energy on the surface of the carbon to overcome the energy needed to adsorb the contaminant.
Contaminants that are organic, have high molecular weights, and are neutral, or non-polar, in their chemical nature are readily adsorbed on activated carbon. For water adsorbates to become physically adsorbed onto activated carbon, they must both be dissolved in water so that they are smaller than the size of the carbon pore openings and can pass through the carbon pores and accumulate.
Besides physical adsorption, chemical reactions can occur on a carbon surface. One such reaction is chlorine removal from water involving the chemical reaction of chlorine with carbon to form chloride ions.
The most important application of activated carbon
The most important application of activated carbon adsorption where large amounts of activated carbons are being consumed and where the consumption is ever increasing is the purification of air and water. There are two types of adsorption systems for the purification of air.
One is the purification of air for immediate use in inhabited types of adsorption systems for the purification of air. One is the purification of air for immediate use in inhabited spaces, where free and clean air is a requirement. The other system prevents air pollution of the atmosphere from industrial exhaust streams.
The former operates at pollutant concentrations below 10 ppm, generally about 2 to 3 ppm. As the concentration of the pollutant is low, the adsorption filters can work for a long time and the spent carbon can be discarded, because regeneration may be expensive.
Air pollution control requires a different adsorption setup to deal with larger concentrations of the pollutants.
The saturated carbon needs to be regenerated by steam, air, or nontoxic gaseousregenerated by steam, air, or nontoxic gaseous treatments. These two applications require activated carbons with different porous structures. The carbons required for the purification of air in inhabited spaces should be highly microporous to affect greater adsorption at lower concentrations. In the case of activated carbons for air pollution control, the pores should have higher adsorption capacity in the concentration range 10 to 500 ppm.
Marketing of activated carbon
Market The global activated carbon industry is estimated to be around 1.1 million metric ton. Demand for virgin activated carbon is expected to rise by around 10% annually through 2014, worldwide. The U.S is the largest market, which will also pace global growth based on anticipated new federal regulations mandating mercury removal at coal- fired power plants. Nearly 80% of the total active carbon is consumed forfired power plants.
Nearly 80% of the total active carbon is consumed for liquid-phase applications, and the gas-phase applications consume about 20% of the total production. Because the active carbon application for the treatment of waste water is picking up, the production of active carbons is always increasing.
The consumption of activecarbon is the highest in the U.S. and Japan, which together consume two to four times more active carbons than European and other Asian countries. The per capita consumption of active carbons per year is 0.5 kg in Japan, 0.4 kg in the U.S., 0.2 kg in Europe, and 0.03 kg in the rest of the world. This is due to the fact that Asian countries by and large have not started using active carbons for water and air pollution control purposes in large quantities.