PRIVATE WELL WATER
IN CONNECTICUT
Publication Date: May 2018
Publication #1: Granular Activated Carbon
Treatment of Private Well Water
Introduction
Granular activated carbon (GAC) is a type of water treatment commonly used to remove chemical contaminants and for taste and odor control. GAC filters come in a variety of types and sizes and can be used to treat the water at a single tap or all the water in your home. As with all treatment types, GAC units must be operated and maintained properly to ensure the water supplying your home remains safe.
GAC can be used to remove or reduce:
- Unwanted tastes and odors
- Radon
- Organic chemicals
- Pesticides and Herbicides
- Chlorine
- Per- and Polyfluoroalkyl Substances (PFAS)
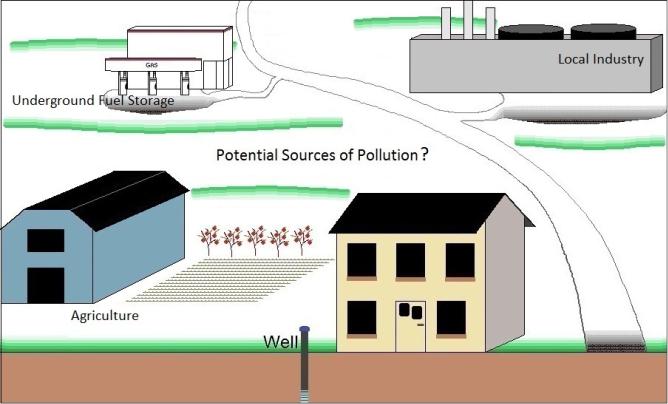
GAC is not considered effective to remove or reduce:
Microorganisms (i.e. bacteria, viruses) Some metals
Nitrates
How Granular Activated Carbon Treatment Works
GAC media is an effective adsorbent because it is highly porous and provides a large surface area for contaminants to adsorb onto. GAC media is made by heating a carbon source such as coal, coconut shells, wood or peat. GAC media is placed inside a filter tank. When untreated water passes through, certain contaminants are attracted to the media and become adsorbed by its surface, becoming trapped in its pores.
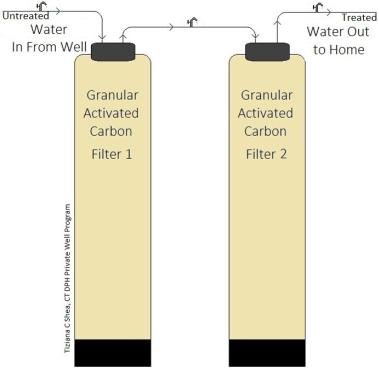
The effectiveness of any GAC filter unit will depend on the type of GAC media installed, the concentration and type of contaminants in the water, and the size of the GAC filter.
Types of Units
GAC filters come in both whole house (also known as point-of- entry (POE)) units and point-of-use (POU) units, which refers to the location where the treatment unit is installed.

Produced by The State of Connecticut Department of Public Health Environmental Health Section, Private Well Program 410 Capitol Avenue, MS#11PWP, PO Box 340308, Hartford, CT 06134 Phone: 860-509-8401 Fax: 860-509-7295
Page 1 of Publication #1: Granular Activated Carbon Treatment of Private Well Water
POU units treat water only at a specific tap ; usually the kitchen sink to treat the water you drink and cook with. POU units can be pour through units, faucet mount units, in-line devices, or line bypass units:
Pour-through GAC units: Untreated water is poured into the top of the pitcher, then passes through a small carbon filter. Treated water is collected at the base of the pitcher. These units are not connected to the water supply and usually sit on counter tops. Pour-through devices only treat small quantities of water at a given time, and are not recommended for removal of organic chemicals.
Faucet mount units are attached to the faucet or placed on the counter with connections to the faucet. Some of these units may be equipped with a bypass option to selectively filter water (usually for cooking and drinking) which helps to prolong the life of the carbon cartridge. Faucet-mount units are typically not recommended for removal of organic chemicals. Certain faucet mount units may be effective at reducing lead in water. Always consult with manufacturer’s specifications to determine effectiveness against specific contaminanants in your water.
The line-bypass unit is attached to the cold water plumbing beneath the kitchen sink and has a separate faucet installed that provides treated water for uses such as cooking and drinking. The regular tap delivers untreated water. This design may increase the life expectancy of the carbon by allowing a choice of either treated or untreated water.
The in-line device is installed beneath the kitchen sink on the cold water plumbing to treat water for uses such as drinking or cooking. If both hot and cold water come from a single faucet, the treated cold water can mix with the untreated hot water. Treated water is provided only when using cold water for uses such as drinking and cooking.
Whole House Treatment (POE) GAC units are typically installed where the water line enters your house and will treat all the water in your household plumbing.
Whole house treatment or POE is recommended for treatment of most volatile organic compounds (VOCs), pesticides, herbicides or chemicals. Whole house treatment also prevents the inhalation of hazardous vapors for those contaminants that can easily vaporize from water into air, such as radon and VOCs. Whole house treatment also prevents skin absorption from bathing and showering from chemicals such as VOCs, pesticides and herbicides.
Unit Effectiveness
The effectiveness of a GAC unit depends on the time of contact between the carbon and the untreated water. The longer the contact time, the better the adsorption of contaminants onto the GAC filter media. Over time, channels can form within the GAC filter media, which may allow some untreated water to pass through the filter media through these channels. Since treatment depends on the GAC media adsorbing the chemical contaminants, these channels decrease the effectiveness of the GAC filter unit.
Some types of GAC filters are better at treating for certain contaminants than others. Discuss your options with a GAC product distributor or water treatment company. Always confirm that the treatment unit you are choosing has been tested to meet manufacturer’s claims.
In order for GAC filtration to be most effective, it is important to follow manufacturer’s maintenance requirements. Filter media should be replaced over time as needed. Consult with your water treatment company installing the GAC treatment unit or the manufacturer to determine maintenance requirements.
Page 2 of Publication #1: Granular Activated Carbon Treatment of Private Well Water
Backwash Wastewater Generated
Treatment backwash is sometimes necessary to lift the GAC filter media and reduce sediment from it.
This process may help eliminate any channels that may have formed in the filter media.
If you have an on-site septic system, water treatment wastewater must be discharged in accordance with criteria established in the CT Department of Public Health, 2018 On-site Disposal Regulations and Technical Standards for Subsurface Sewage Disposal Systems.
Contact CT Department of Energy and Environmental Protection if you are connected to municipal sewer and the WPCA does not allow discharge of treatment backwash water to the sewer.
Maintenance
Water treatment equipment will not perform satisfactorily unless it is maintained in accordance with manufacturer’s recommendations for maintenance, cleaning and part replacement. It is recommended that you keep a record of equipment maintenance and repairs.
GAC filter units need to have the GAC media inside changed regularly. For small point of use specialty units, the entire cartridge filter is normally replaced. POE GAC filters are often used in line with a pre-treatment filter to remove sediment and iron particles that can clog the carbon filter. If installed, pre-treatment filters will also need to be replaced periodically.
GAC filter media eventually becomes saturated and can no longer adsorb contaminants. This is called ‘breakthrough’. When this occurs, the GAC filter media can no longer remove contaminants from the water. If left for too long after this point, contaminant concentration levels in the water supplying your house could actually be higher than the untreated water entering the GAC filter. Two GAC filters may be placed in series to prevent breakthrough contaminants from reaching your home’s water supply. Changing the filter media on a regular basis will also help to prevent breakthrough from occurring.
GAC maintenance frequency will vary based on the size of the filter unit, household water usage, contaminant concentration levels, and overall water quality. Water quality testing can help determine when GAC media needs to be replaced. A water meter installed at the filter may be helpful in determining when carbon replacement is necessary. Refer to the two sections below for more information.
GAC media can sometimes provide a medium for bacterial growth, reducing the effectiveness of the filter. If bacterial growth coats your GAC media it may also enter your household plumbing system. If test results indicate bacteria is present in the water, replacement of the GAC filter media and disinfection of your well water and household plumbing may be needed. Use of GAC media infused with an antibacterial coating to help prevent bacterial growth may also be considered.
Depending on the types and concentrations of the contaminant being removed, GAC filter media may require special waste handling and disposal. Ask your water treatment company beforehand about disposal costs, disposal requirements and whether alternative treatment methods should be considered before making a decision to install a GAC treatment system.
Alternative options may include use of bottled water, installing a new well in another location that is not contaminated, or connecting to a public water system when available and feasible. Using bottled water for drinking and cooking may be an option, however, when contaminant levels are high, or, pose a risk during bathing and showering, whole house GAC treatment may be the best option. In many cases use of bottled water can serve as a viable temporary solution until a long term solution has been made.
Page 3 of Publication #1: Granular Activated Carbon Treatment of Private Well Water
GAC Unit Installation and Water Testing Considerations
Always confirm with your water treatment installer that your GAC unit is installed according to manufacturer’s specifications. Retain a copy of your GAC unit manufacturer’s specifications for reference and follow any required maintenance protocols. Confirm with your water treatment installer that all State and Local requirements will be met during its installation.
After installation, test both the untreated water (raw water from the well) and treated water (water after GAC treatment) at a state certified laboratory. Compare the results of the treated and untreated water to determine if the GAC unit is properly removing contaminants. Test untreated and treated water annually or more frequently if high levels of contaminants are present in the untreated water. Frequent testing will help you determine how well your treatment system is working and whether maintenance or replacement of components may be necessary.
It is a good idea to install sample taps before (pre) and after (post) GAC filtration. Periodic testing both pre and post filter will help determine when the filter media needs to be changed and to ensure that breakthrough hasn’t occurred. Installing a water meter and recording water meter readings when new filter GAC media is added can also help determine about how many gallons the GAC filter treated before service was needed. You can then use this number to estimate approximately how many gallons the GAC filter can treat before it is no longer effective and how often you should test water quality after filtration to determine if breakthrough has occurred.
If you have two GAC filters installed in series, sample taps can be installed pre, mid and post GAC filtration. Periodic testing can be performed pre, mid and post filtration to determine when service is needed or if breakthrough has occurred. Once the mid -stream water quality sample indicates that the GAC filter media should be changed, the second GAC filter is often times swapped to the front position and a filter with new GAC media is moved to the second filter position.
Questions to Ask Before you Buy
Before purchasing a water treatment device, have your water tested at a state certified laboratory to determine the contaminants present and their concentrations. This will help you determine if GAC is an effective treatment method for the water quality parameters identified through the test results. See Publication #19: Questions to Ask When Purchasing Water Treatment Equipment, for more information.
For More Information:
Please contact the Connecticut DPH, Private Well Program at 860-509-8401.
Page 4 of Publication #1: Granular Activated Carbon Treatment of Private Well Water