Because of activated charcoal’s incredible adsorption ability, it is an ideal choice for air and water filters. When used appropriately, charcoal filters will effectively clean the air and water by electrostatically binding pollutants to its vast surface area.
Many people use activated charcoal filters in outdoor ponds and aquariums to keep the water clean and the marine life healthy.
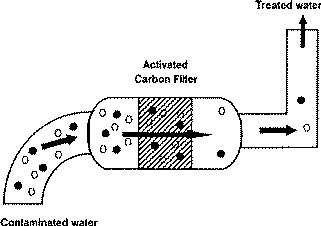
Carbon filtering is a method of filtering that uses a bed of activated carbon to remove contaminants and impurities, using chemical absorption.
Each particle/granule of carbon provides a large surface area/pore structure, allowing contaminants the maximum possible exposure to the active sites within the filter media. One pound (450 g) of activated carbon contains a surface area of approximately 100 acres (40 Hectares).
Activated carbon works via a process called adsorption, whereby pollutant molecules in the fluid to be treated are trapped inside the pore structure of the carbon substrate. Carbon filtering is commonly used forwater purification, in air purifiers and industrial gas processing, for example the removal of siloxanes and hydrogen sulfide from biogas. It is also used in a number of other applications, including respirator masks, the purification of sugarcane and in the recovery of precious metals, especially gold. It is also used in cigarette filters.
Active charcoal carbon filters are most effective at removing chlorine, sediment, volatile organic compounds (VOCs), taste and odor from water. They are not effective at removing minerals, salts, and dissolved inorganic compounds.
What carbon filtration doesn’t do can be seen in the remaining three categories of the EPA contaminant list. Carbon is mentioned as a treatment for only one of the four Microbiological contaminants listed: turbidity.
It is not recommended for coliform removal or for cysts, though ironically, some of the very tight solid carbon block filters now on the market remove bacteria (though manufacturers seldom make this claim) and cysts like giardia and cryptosporidium quite handily. Multipure solid carbon blocks, in fact, were the first filtration device certified by NSF (the most prestigious independent agency that tests and certifies product performance) for removal of cryptosporidium.
Multipure and some other very tight carbon block filters remove cysts simply because of their restricted pore size. Multipure blocks are absolute 1/2 micron filters, making cryptosporidium organisms about ten times too fat to go through the holes. Thus, although other types of very tight filtration might work as well, the very dense carbon block filters now on the market are very effective against certain forms of microbiological contaminants.
Activated Carbon for drinking water Treatment
Potable or drinking water is a commodity with stringent requirements of being safe and pure. Granular Activated Carbons (GACs) and Powder Activated Carbons (PACs) is your ideal solution in making drinking water free from taste and odor forming compounds such as MIB and geosmin, undesired colors, endocrine disrupting compounds and other micropollutants, chlorinated hydrocarbons, Trihalomethanes and other disinfection byproducts, VOCs, pesticides and their byproducts.
You can treat drinking water with the high quality, standard, and specially processed products complying with NSF 61, NSF 42, PROP 65 certifications with low dechlorination half values, superior flow characteristics, consistent particle size distributions to facilitate pressure drop and adsorption kinetics requirements, extensive pore structures with an ideal balance of both adsorption and transport pores, and high mechanical strength resulting in minimal operational and pressure drop issues. These superior features have made granular carbon products the industry choice for Point of Use (POU) and Point of Entry (POE) water filters.
Activated Carbon for Municipality water treatment
In the treatment of municipal water, removal of organics including VOCs, inorganics and toxins inherent in the rivers, lakes, reservoirs and other surface water sources and ground water systems is essential. You can find a tailor made series of products for surface and ground water treatment in municipality water treatment systems to deliver consistent performance in removing these contaminants.
These products are also geared to adsorb hazardous pesticide and herbicide residues, chlorinated hydrocarbons, disinfectant byproducts, inhibitory compounds for biological treatment systems, non-biodegradable organic compounds, and undesired colored and smell compounds. Our carbons are effective in lowering of Biochemical Oxygen Demand (BOD), Chemical Oxygen Demand (COD), Total Organic Content (TOC) and toxicity. In addition, the high purity of the carbon products prevents the release of contaminants that may damage sensitive membrane systems used in other in-process filtration systems. We also offer custom designed products and total purification solutions to best suit your requirement.