Graphene is a crystalline allotrope of carbon with 2-dimensional properties. Its carbon atoms are densely packed in a regular atomic-scale chicken wire (hexagonal) pattern. Each atom has four bonds, one σ bond with each of its three neighbors and one π-bond that is oriented out of plane. The atoms are about 1.42 Å apart.
Graphene’s hexagonal lattice can be regarded as two interleaving triangular lattices. This perspective was successfully used to calculate the band structure for a single graphite layer using a tight-binding approximation。Graphene is amazing. Or at least, it could be. Made from a layer of carbon one-atom thick, it’s the strongest material in the world, it’s completely flexible, and it’s more conductive than copper. Discovered just under a decade ago, the supermaterial potentially has some unbelievable applications for us in the not so distant future.
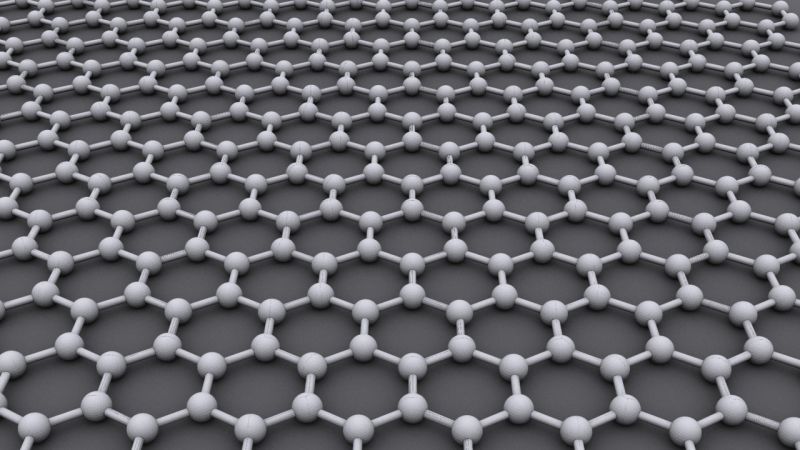
Graphene, the well-publicised and now famous two-dimensional carbon allotrope, is as versatile a material as any discovered on Earth. Its amazing properties as the lightest and strongest material, compared with its ability to conduct heat and electricity better than anything else, mean that it can be integrated into a huge number of applications. Initially this will mean that graphene is used to help improve the performance and efficiency of current materials and substances, but in the future it will also be developed in conjunction with other two-dimensional (2D) crystals to create some even more amazing compounds to suit an even wider range of applications. To understand the potential applications of graphene, you must first gain an understanding of the basic properties of the material.
The first time graphene was artificially produced; scientists literally took a piece of graphite and dissected it layer by layer until only 1 single layer remained. This process is known as mechanical exfoliation. This resulting monolayer of graphite (known as graphene) is only 1 atom thick and is therefore the thinnest material possible to be created without becoming unstable when being open to the elements (temperature, air, etc.). Because graphene is only 1 atom thick, it is possible to create other materials by interjecting the graphene layers with other compounds (for example, one layer of graphene, one layer of another compound, followed by another layer of graphene, and so on), effectively using graphene as atomic scaffolding from which other materials are engineered. These newly created compounds could also be superlative materials, just like graphene, but with potentially even more applications.
After the development of graphene and the discovery of its exceptional properties, not surprisingly interest in other two-dimensional crystals increased substantially. These other 2D crystals (such as Boron Nitride, Niobium Diselenide and Tantalum (IV) sulphide), can be used in combination with other 2D crystals for an almost limitless number of applications. So, as an example, if you take the compound Magnesium Diboride (MgB2), which is known as being a relatively efficient superconductor, then intersperse its alternating boron and magnesium atomic layers with individual layers of graphene, it improves its efficiency as a superconductor. Or, another example would be in the case of combining the mineral Molybdenite (MoS2), which can be used as a semiconductor, with graphene layers (graphene being a fantastic conductor of electricity) when creating NAND flash memory, to develop flash memory to be much smaller and more flexible than current technology, (as has been proven by a team of researchers at the École Polytechnique Fédérale de Lausanne (EPFL) in Switzerland).
The only problem with graphene is that high-quality graphene is a great conductor that does not have a band gap (it can’t be switched off). Therefore to use graphene in the creation of future nano-electronic devices, a band gap will need to be engineered into it, which will, in turn, reduce its electron mobility to that of levels currently seen in strained silicon films. This essentially means that future research and development needs to be carried out in order for graphene to replace silicon in electrical systems in the future. However, recently a few research teams have shown that not only is this possible, it is probable, and we are looking at months, rather than years, until this is achieved at least at a basic level. Some say that these kinds of studies should be avoided, though, as it is akin to changing graphene to be something it is not.
In any case, these two examples are just the tip of the iceberg in only one field of research, whereas graphene is a material that can be utilized in numerous disciplines including, but not limited to: bioengineering, composite materials, energy technology and nanotechnology.
Mechanical strength
Graphene is the world’s strongest material, and so can be used to enhance the strength of other materials. Dozens of researches have demonstrated that adding even a trade amount of graphene to plastics, metals or other materials can make these materials much stronger – or lighter (as you can use less amount of material to achieve the same strength).
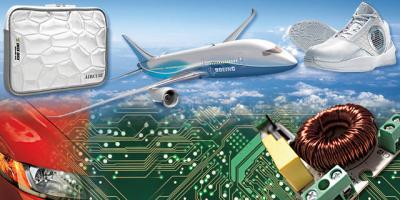
Thermal applications
Graphene is the world’s most conductive material to heat. As graphene is also strong and light, it means that it is a great material to make heat-spreading solutions, such as heat sinks. This could be useful in both microelectronics (for example to make LED lighting more efficient and longer lasting) and also in larger applications – for example thermal foils for mobile devices.
Biological Engineering
Bioengineering will certainly be a field in which graphene will become a vital part of in the future; though some obstacles need to be overcome before it can be used. Current estimations suggest that it will not be until 2030 when we will begin to see graphene widely used in biological applications as we still need to understand its biocompatibility (and it must undergo numerous safety, clinical and regulatory trials which, simply put, will take a very long time). However, the properties that it displays suggest that it could revolutionise this area in a number of ways. With graphene offering a large surface area, high electrical conductivity, thinness and strength, it would make a good candidate for the development of fast and efficient bioelectric sensory devices, with the ability to monitor such things as glucose levels, haemoglobin levels, cholesterol and even DNA sequencing. Eventually we may even see engineered ‘toxic’ graphene that is able to be used as an antibiotic or even anticancer treatment. Also, due to its molecular make-up and potential biocompatibility, it could be utilised in the process of tissue regeneration.
Optical Electronics
One particular area in which we will soon begin to see graphene used on a commercial scale is that in optoelectronics; specifically touchscreens, liquid crystal displays (LCD) and organic light emitting diodes (OLEDs). For a material to be able to be used in optoelectronic applications, it must be able to transmit more than 90% of light and also offer electrical conductive properties exceeding 1 x 106 Ω1m1 and therefore low electrical resistance. Graphene is an almost completely transparent material and is able to optically transmit up to 97.7% of light. It is also highly conductive, as we have previously mentioned and so it would work very well in optoelectronic applications such as LCD touchscreens for smartphones, tablet and desktop computers and televisions.
Currently the most widely used material is indium tin oxide (ITO), and the development of manufacture of ITO over the last few decades time has resulted in a material that is able to perform very well in this application. However, recent tests have shown that graphene is potentially able to match the properties of ITO, even in current (relatively under-developed) states. Also, it has recently been shown that the optical absorption of graphene can be changed by adjusting the Fermi level. While this does not sound like much of an improvement over ITO, graphene displays additional properties which can enable very clever technology to be developed in optoelectronics by replacing the ITO with graphene. The fact that high quality graphene has a very high tensile strength, and is flexible (with a bending radius of less than the required 5-10mm for rollable e-paper), makes it almost inevitable that it will soon become utilized in these aforementioned applications.
In terms of potential real-world electronic applications we can eventually expect to see such devices as graphene based e-paper with the ability to display interactive and updatable information and flexible electronic devices including portable computers and televisions.
Coatings ,sensors, electronics and more
Graphene has a lot of other promising applications: anti-corrosion coatings and paints, efficient and precise sensors, faster and efficient electronics, flexible displays, efficient solar panels, faster DNA sequencing, drug delivery, and more.
Graphene is such a great and basic building block that it seems that any industry can benefit from this new material. Time will tell where graphene will indeed make an impact – or whether other new materials will be more suitable.
Ultrafiltration
Another standout property of graphene is that while it allows water to pass through it, it is almost completely impervious to liquids and gases (even relatively small helium molecules). This means that graphene could be used as an ultrafiltration medium to act as a barrier between two substances. The benefit of using graphene is that it is only 1 single atom thick and can also be developed as a barrier that electronically measures strain and pressures between the 2 substances (amongst many other variables). A team of researchers at Columbia University have managed to create monolayer graphene filters with pore sizes as small as 5nm (currently, advanced nanoporous membranes have pore sizes of 30-40nm). While these pore sizes are extremely small, as graphene is so thin, pressure during ultrafiltration is reduced. Co-currently, graphene is much stronger and less brittle than aluminium oxide (currently used in sub-100nm filtration applications). What does this mean? Well, it could mean that graphene is developed to be used in water filtration systems, desalination systems and efficient and economically more viable biofuel creation.
Composite Materials
Graphene is strong, stiff and very light. Currently, aerospace engineers are incorporating carbon fibre into the production of aircraft as it is also very strong and light. However, graphene is much stronger whilst being also much lighter. Ultimately it is expected that graphene is utilized (probably integrated into plastics such as epoxy) to create a material that can replace steel in the structure of aircraft, improving fuel efficiency, range and reducing weight. Due to its electrical conductivity, it could even be used to coat aircraft surface material to prevent electrical damage resulting from lightning strikes. In this example, the same graphene coating could also be used to measure strain rate, notifying the pilot of any changes in the stress levels that the aircraft wings are under. These characteristics can also help in the development of high strength requirement applications such as body armour for military personnel and vehicles.
Photovoltaic Cells
Offering very low levels of light absorption (at around 2.7% of white light) whilst also offering high electron mobility means that graphene can be used as an alternative to silicon or ITO in the manufacture of photovoltaic cells. Silicon is currently widely used in the production of photovoltaic cells, but while silicon cells are very expensive to produce, graphene based cells are potentially much less so. When materials such as silicon turn light into electricity it produces a photon for every electron produced, meaning that a lot of potential energy is lost as heat. Recently published research has proved that when graphene absorbs a photon, it actually generates multiple electrons. Also, while silicon is able to generate electricity from certain wavelength bands of light, graphene is able to work on all wavelengths, meaning that graphene has the potential to be as efficient as, if not more efficient than silicon, ITO or (also widely used) gallium arsenide. Being flexible and thin means that graphene based photovoltaic cells could be used in clothing; to help recharge your mobile phone, or even used as retro-fitted photovoltaic window screens or curtains to help power your home.
Energy Storage
Because graphene is the world’s thinnest material, it is also the material with the highest surface-area to volume ratio. This makes graphene a very promising material to be used in batteries and supercapacitors. Graphene may enable devices that can store more energy – and charge faster, too. Graphene can also be used to enhance fuel-cells. While all areas of electronics have been advancing over a very fast rate over the last few decades (in reference to Moore’s law which states that the number of transistors used in electronic circuitry will double every 2 years), the problem has always been storing the energy in batteries and capacitors when it is not being used. These energy storage solutions have been developing at a much slower rate. The problem is this: a battery can potentially hold a lot of energy, but it can take a long time to charge, a capacitor, on the other hand, can be charged very quickly, but can’t hold that much energy (comparatively speaking). The solution is to develop energy storage components such as either a supercapacitor or a battery that is able to provide both of these positive characteristics without compromise.
Currently, scientists are working on enhancing the capabilities of lithium ion batteries (by incorporating graphene as an anode) to offer much higher storage capacities with much better longevity and charge rate. Also, graphene is being studied and developed to be used in the manufacture of supercapacitors which are able to be charged very quickly, yet also be able to store a large amount of electricity. Graphene based micro-supercapacitors will likely be developed for use in low energy applications such as smart phones and portable computing devices and could potentially be commercially available within the next 5-10 years. Graphene-enhanced lithium ion batteries could be used in much higher energy usage applications such as electrically powered vehicles, or they can be used as lithium ion batteries are now, in smartphones, laptops and tablet PCs but at significantly lower levels of size and weight.